here comes the sun
story by Neil Caudle and feature photo by Annemarie Jacques
How thrifty can a building be? We’re about to find out.
how to learn from a building
Lee 3 is designed to test and expand current knowledge of sustainable design and construction.
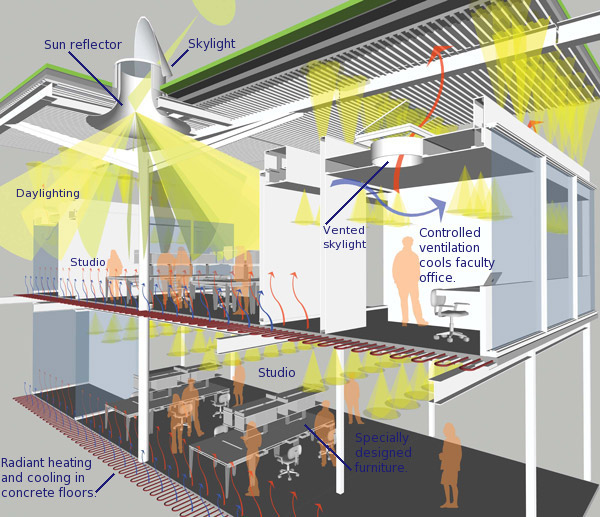
Monitored electrical circuits will report energy use to an electronic dashboard so that students and faculty members can access real-time data on energy consumption. Teams of students will investigate how to operate the building with the least possible energy purchased from the grid. The dashboard’s computer will also monitor water use, indoor and outdoor temperature and humidity, and pollen levels.
Energy savings began with the decision to use construction materials, some with recycled content, available from sources within 500 miles of the site. This reduced the carbon footprint of the project, a prime goal of sustainability.
Approximately 72,000 linear feet of 5/8-inch tubing carries liquid through the slabs, heating or cooling the building. Forty-two geothermal wells installed to a depth of 440 feet provide approximately 80 tons of heating and cooling and allow Lee 3 to operate without taking energy from the coal-based campus plant.
3 degrees of Lee
With its leap toward the future, its courtyards, and its emphatic choice to work with nature rather than against it, Lee 3 takes some DNA from Lee 1, designed by then Dean of Architecture Harlan McClure and opened in 1958.
Wrapped around a shady courtyard favored for exhibits and conversation, Lee 1 was the green building of its day, with louvers and operable windows for ventilation and with abundant natural light.
Lee Hall was also the first modernist building on campus, a then-radical design that has since become classic, earning a place on the National Register of Historic Places. Lee 2, completed in 1975, did its job—adding growing room. Today, a portion of Lee 2 has been reconfigured along Broadway, an expansive indoor avenue with alcoves for teaching and exhibits, linking Lee 1 to Lee 3. McMillan Pazdan Smith Architecture of Greenville, South Carolina, was the local architecture firm of record for the work on Lee 3 and the renovations of Lee 2.
In the corners of Lee 3, small red bulbs are glowing. This means: Keep the windows closed. Today is a red-light day, the weather gray and cold. But when spring arrives and sunlight heats the space inside, the lights will switch from red to green. Rows of awning windows near the roof will swing open, prompted by a vigilant computer. Then students and faculty members will stop what they are doing and open, with their hands, corresponding sets of windows near the floor. Convection—the chimney effect that once aired Southern houses—will draw fresh, cool air through the low windows and purge warm, stale air through the high ones.
This is what people did a hundred years ago; they opened the windows. But today? Can actual occupants be trusted to operate an expensive public building? It’s almost unthinkable.
And yet this is what Lee 3 requires.
“This building is a machine,” says Robert Silance, associate professor of architecture. “It doesn’t just sit there. When that light goes green and those windows open, is that an intrusion? We don’t know yet. The building is asking us to change how we behave.”
For years, students have been sketching and groping their way toward buildings like this—open, distinctive structures with precious little use for fossil fuel; buildings that would ask more of the inhabitants but give more in return. And now the students can work in one.
Measuring up
Tom Phifer was a student here once, learning his chops in the studios of the original Lee Hall, known today as Lee 1. Now a big-time architect and the lead designer for Lee 3, Phifer has set the bar high. The stunning new building, when equipped with a full array of photovoltaic panels, could produce as much energy as it needs. A few years ago, this was the future, theoretical and safely remote. Suddenly it is here.
“The building is way ahead of us,” Silance says. “Everybody’s expectations are higher now. We will have to measure up.”
Part of measuring up has meant furnishing the building to function as intended. With a team of students and colleagues, Silance designed tables and workstations in several configurations and had them fabricated by Sargent Metals of Anderson and Design Solutions, Inc. of Chapin, S.C. On a campus bound by state-government purchasing rules, this took some doing, but the goal of sustainability meant using local suppliers with a stake in the local economy. The team also wanted furniture that encouraged group projects, not isolation.
“The desks became more than desks,” says Daniel Harding, a colleague who worked on the project. “They are fixtures of collaboration.”
Collaboration will be one measure of success for Lee 3, which will house architects, planners, landscape architects, construction-management experts, real-estate developers, and others. All of them will have adjustments to make.
“The building has such a strong presence that you can get infatuated with it as an object,” Harding says. “But it’s not so much what the buildingis as what it does, what it engenders. We’ll need to grow into it and not disrespect it.”
With all due respect
Disrespect might include, for example, carving open spaces into enclaves for holing up and hiding out, or covering the floors with clutter that could interfere with the flow of radiant heating and cooling from the concrete slabs.
But respect in the case of Lee 3 isn’t strictly hands-off. Paul Russell, a landscape architecture professor, wondered at first what to make of a classroom nakedly exposed to adjacent spaces, its most prominent wall made of windows. His solution: a dry-erase marker. Now, when he teaches, people stop to watch him draw on the glass.
Nor is the assignment of spaces sacrosanct. The faculty lounge, with a northern exposure ideal for drawing, may eventually give way to review space. Harding, who has long admired the sunny porches of old Southern houses, plans to roll a canopied coffee cart into an interior courtyard and see who gathers there to take the sun and swap ideas.
The whole of Lee 3 is a laboratory of sorts, and its occupants will run experiments on the building and themselves, learning what works and what doesn’t. Whatever direction those experiments take, they will proceed in the open. There is no place to hide in this place, where even the pipes are exposed.
“For some people, the transparency of the building is a little scary,” Russell says. “But I like it and expect it will make us all do better work.”
Robert Silance, associate professor of architecture, conducts research in product and furniture design. Daniel Harding is an associate professor of architecture and director of the Community Research and Design Center. Paul Russell is an assistant professor in planning and landscape architecture. The firm of Thomas Phifer and Partners, based in New York City, has designed many internationally prominent buildings, including the North Carolina Museum of Art in Raleigh.
bringing it home
Mary Catalanotto Parker
Prize-winning teams zero in on housing.

Eric Laine and Suzanne Steelman took first place in the Design to Zero competition with a design that integrated commercial and residential spaces.
How much energy does it take to run a house? How about none?
That’s no pipe dream, according to Ulrike Heine, assistant professor of architecture. Heine and her students design zero-energy houses for the Southeast.
“When we talk about sustainable architecture,” Heine says, “we mean architecture that acts with and takes advantage of the laws of nature.”
In February two teams of Clemson graduate students from Heine’s design studio took first and second place in Design to Zero, an international competition sponsored by Dow Chemical Company. Three additional Clemson teams also received awards. The competition, whose objective was to design affordable, energy-efficient housing, included 131 design teams from 19 countries. Peers ranked the entries.
Here are Clemson’s winners:
- The Live/Work team, Eric Laine and Suzanne Steelman, won first place and $20,000 with a sleek design that incorporates both commercial and residential functions.
- Daniel Kim and Caitlin Ranson won second place and $10,000 for their Project Zero design, which blurs the boundaries between interior and exterior spaces.
- Honorable Mention went to John Oxenfeld and Adam Wilson for their Partial Submersion design.
- Mike Niezer and Adrian Mora took the Design Integration Award for crafting a serene and clean breathZero house.
- The Built-In Photovoltaic Design Award went to Jason Drews and James Graham for their Below Zero design with optimal solar angles.
The winning teams drew on contemporary research in a range of fields, Heine says. Her colleagues Daniel Harding and Bernard Sill advised students on questions of community design, residential construction, and structural systems.
Designing a zero-energy house requires a scientific understanding of environment and materials, Heine says, and students learn to calculate the carbon footprint of various building materials. They begin their research by asking the right questions, such as, “How can a sustainable house beat the rugged humidity of South Carolina?” They review data from field research into climate, materials, and engineering and construction methods, often drawing on the studies of Clemson researchers who work outside of architecture.
“We have all the players here,” says Kate Schwennsen, chair of the School of Architecture, “from material science to construction science to civil engineering, and all those disciplines are key to advancing what we know.”