Making cars lighter, stronger
Taylor Reeves
With gas prices soaring, the auto industry is looking for ways to save fuel and cut emissions. One solution: a lighter car.
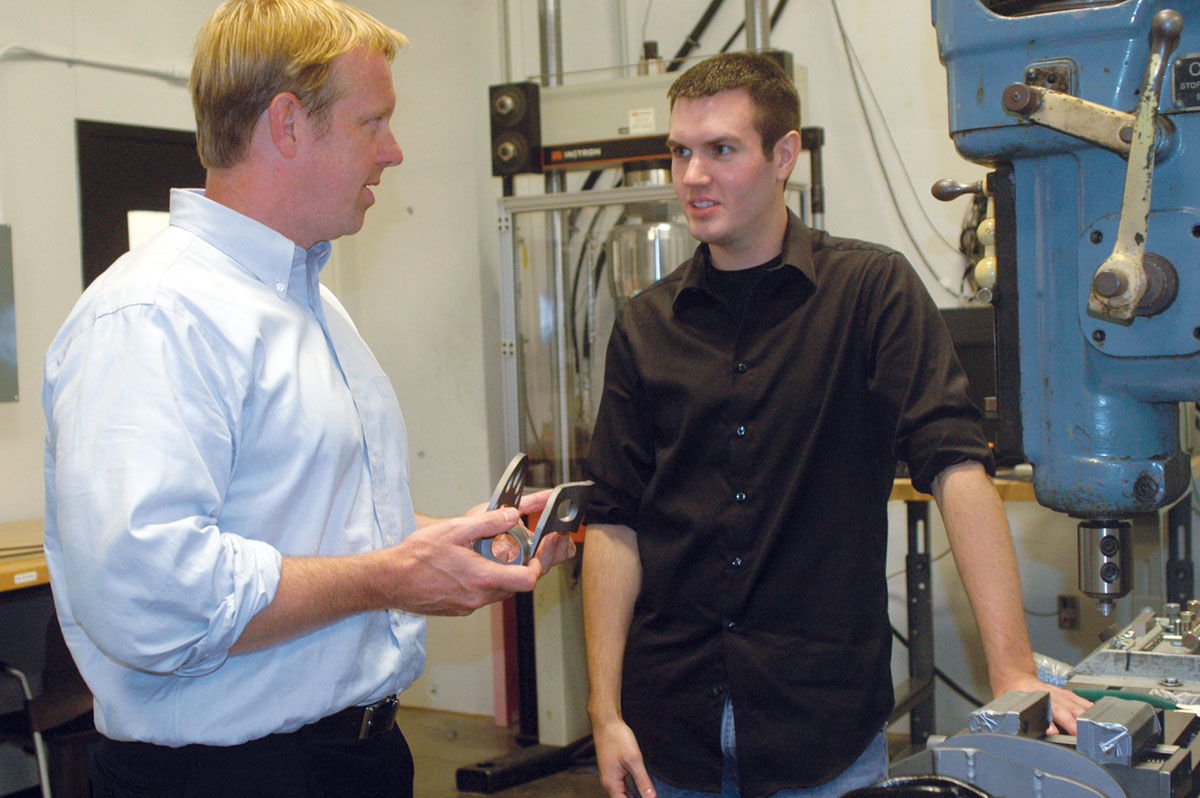
Laine Mears discusses a damper fork with graduate student Joshua Jones. Image courtesy Wanda Johnson.
“The big vision for automotive companies right now is making cars that are lighter weight,” says Laine Mears, automotive engineering professor and researcher with Clemson’s manufacturing group at the International Center for Automotive Research (CU-ICAR). Mears leads a research project sponsored by the U.S. Department of Energy’s Lightweight Automotive Materials Program (LAMP). “The amount of energy it takes to move a car from one point to another is highly dependent on the mass, so the lighter the vehicle, the less energy it takes to move it from one place to another.”
While today’s engines are more fuel-efficient than those of years past, automakers have been packing cars with new features whose extra weight has kept fuel economy roughly the same, Mears says. More stringent fuel-efficiency standards are on the near horizon, requiring changes in technology to improve efficiency.
To help offset vehicle weight, Mears and his team tested an alternative to steel: titanium. Lightweight but strong, titanium is already common in aircraft, armor, missiles, and laptop computers. For the past two years, LAMP researchers at CU-ICAR have been exploring the use of titanium as a feasible material in automobile manufacturing.
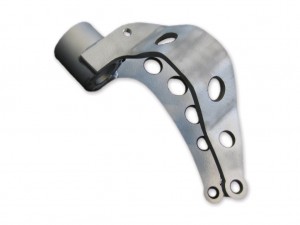
Using titanium in a front damper fork saves weight and fuel, and improves performance. Image courtesy Joshua Jones.
To test the potential, the team worked with BMW to select a part of the vehicle where titanium could both save mass and improve performance: the front damper fork, a suspension component that connects the wheel carrier to the car’s body frame. The team redesigned and built a titanium prototype of the fork and tested it both in the lab and in a vehicle, analyzing strength and dynamic performance, which were improved over the stock component. The team concluded that fuel savings achieved over the life of a vehicle with the titanium component—twenty-two to thirty gallons—could be used to justify its higher initial cost.
Phase two of the project focused on reducing production costs. Titanium’s capacity to absorb heat makes it difficult to manufacture, as machining tools cannot withstand the temperatures necessary to shape it. This temperature increase in the cutting zone causes tools to wear down rapidly during the machining process. To combat these problems, LAMP researchers used the Clemson high-performance computing system to simulate and analyze a wide range of different manufacturing techniques. The system helped the team identify the main causes of tool wear and learn how to manufacture titanium more efficiently.
Another barrier to titanium’s widespread use is availability: The mineral is difficult to mine and costly to produce. But American Titanium Works, a manufacturer in the U.S., plans to build a production facility in Laurens County, South Carolina—an asset to researchers at CU-ICAR as they develop new titanium components and manufacturing methods.
A ten-year veteran of the automotive industry before he joined CU-ICAR in 2006, Mears says that he will keep exploring the potential for using lightweight manufacturing to improve vehicles and increase fuel economy.
“For lightweight manufacturing, there are some fundamental issues we need to get across, not only in manufacturing processes but also in selecting the correct material for the correct function, and bringing different materials together effectively in the vehicle,” he says.
“That’s what this research is all about: getting past those underlying issues so we can see the greater benefit to industry and ultimately to society.”
Laine Mears is an associate professor of automotive engineering at the Clemson University International Center for Automotive Research and a member of the Center for Emerging Technologies. Funding for this research is from the U.S. Department of Energy through the National Center for Manufacturing Sciences.