Defining the Wind
by Neil Caudle

Marvels of technology, centuries removed
This panoramic view shows a 1.6 megawatt nacelle being tested in the smaller of two drive bays, a whopping 7.5 megawatts. Photo by Ryan Schkoda.
How do you tune a huge turbine to the forces of nature and help deploy the next generation of green-energy machines?
Charleston. It’s a city where history loops forward. Where an iron-hulled Civil War submarine, the H. L. Hunley, an engineering marvel of her time, slowly surrenders to science the secrets of her last fateful hours at sea.
Charleston is also a city built in part by the wind. In the early 1700s, Dutch engineers came to the Lowcountry to erect windmills, engineering marvels of their time. From Cape Romain to Edisto Island, coastal breezes spun the lacy blades above the landscape, milling the pine and cypress lumber from which Charleston would rise.Today, you can walk a few steps from the Warren Lasch Conservation Center, where the Hunley steeps in a chemical broth that will leach away her salts and preserve her hull, and enter a space-age, hangar-size building fitted out with enough high-tech hardware to incubate a new generation of engineering marvels: futuristic wind machines. These turbines will not mill pine or cypress. They will not grind corn. But they could spin Charleston full circle and make it, once again, a city attuned to the wind.
If things here in North Charleston go according to plan, no other city in the United States will have a better chance to help put the wind back to work—and not just as a marginal player in a carbon-laden energy market. Wind power, our engineers tell us, has serious, big-time potential. One large turbine, well sited and engineered, could supply the entire Charleston peninsula with power. Imagine what dozens or hundreds could do.
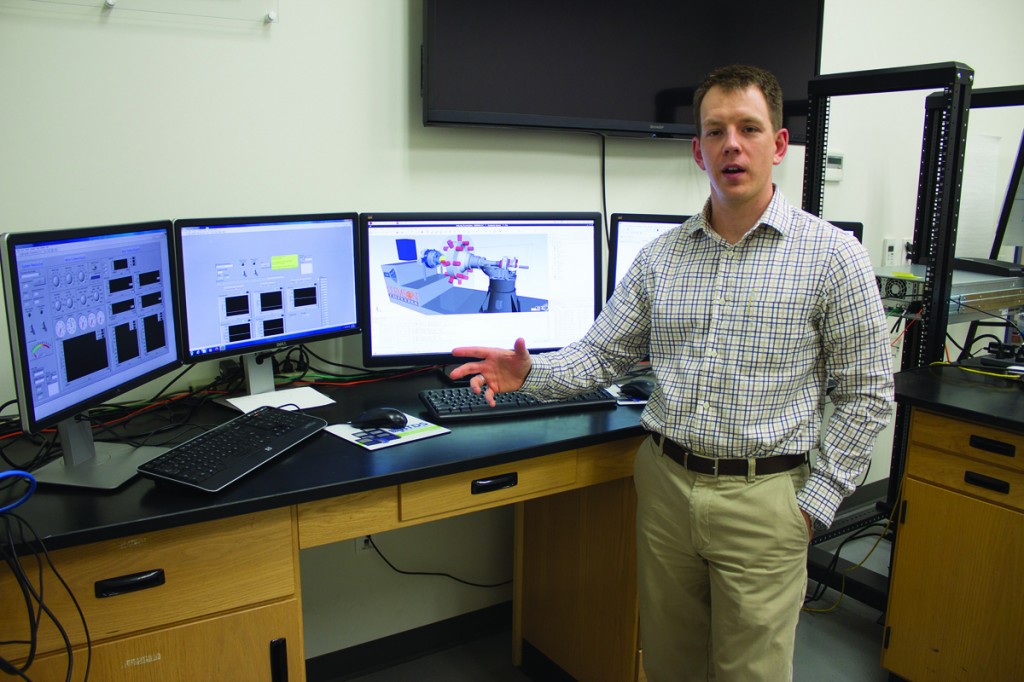
Ryan Schkoda explains the array of computers and displays he uses to model the performance of wind turbines. Photo by Neil Caudle.
Making it work
Some people are not yet convinced that wind is an answer. We have, for the moment, a relatively cheap abundance of fossil fuels and a great deal of costly infrastructure devoted to using them. And some of us don’t like the looks of wind farms, or the politics of the renewable-energy lobby, or the risk to bats and birds that a spinning hub of blades poses. But carbon emissions and a warming climate present their own aesthetic downside, their own risks to bats and birds. So when practical-minded engineers like Ryan Schkoda tune out the pundits and just look at the numbers, and the rapidly evolving technology, and the freely available force of the wind, more and more of them are saying, as the Dutch engineers did three centuries ago, “This will work.”
Schkoda is definitely one of those make-it-work sorts of guys. Having earned a Ph.D. in mechanical engineering from Clemson in 2012, followed by two years of postdoctoral research here, he is now a research scientist and one of several Clemson faculty members based at the wind-turbine testing facility.
And he is the right guy to explain, patiently and clearly, how a great many complex technologies can mesh to yield not only the power of electricity but the power of knowledge.
It’s a job that might almost seem too big for a man so young. Schkoda is the guy at Clemson most responsible for persuading computers to simulate and predict, right down to the last bolt and bearing, the way turbines behave in the wind. That means every imaginable kind of wind, from the gentlest zephyr to a catastrophic hurricane. Schkoda is also the guy most responsible for making sure that, before General Electric or some other corporation goes to the considerable expense of installing one of its enormous new turbines for a test drive in one of the facility’s cavernous bays, the computers and software will be able to put that turbine through its paces in a realistic, reliably informative way. Because if Clemson can’t pull this off, then millions of dollars’ worth of facilities and a whole lot of pent-up potential may well go to waste.
But no pressure, Dr. Schkoda.
Bigger turbines for bigger gains
Let’s take a step back for a moment, from Schkoda’s computer screens full of cockpit-like readouts and graphic animations, and consider the why. Why have the U.S. Department of Energy and various big corporations invested millions in this place, a reclaimed former navy yard in North Charleston, South Carolina? Why do we need a NASA-scale behemoth of a building, packed with so much high-powered electrical muscle that it needs its own substation?
The answer, at its simplest, is that we don’t really know yet the limits of wind power. We don’t really know, exactly, how the next generation of turbines will work. Yes, wind farms are sprouting on ridges and prairies across the United States, supplying, at last count, about 4.3 percent of the nation’s electricity production. But most of these wind farms are land based and use relatively small turbines, usually in the range of 1 to 3 megawatts each. The two bays of Clemson’s facility at Charleston are designed for testing turbines of up to 7.5 and 15 megawatts. Turbines in that range would be a huge leap forward, both in generating capacity and environmental friendliness. Studies by Swiss and Dutch researchers have found that the larger the turbine, the greener the energy it produces.
In the very early days, large wind turbines had a spotty record. One 131-foot-tall monster, mounted by NASA on Howard’s Knob in Boone, North Carolina, in 1977, made a whooshing sound that rattled windows and annoyed the locals; it was dismantled in 1983. Wind-turbine technology has come a long, long way since then. And from an engineer’s point of view, it seems likely, given today’s rapidly advancing technology, that the next generation of big turbines will produce power more efficiently and more economically than small turbines can, especially offshore, where each installation requires securing a tower to the sea floor and protecting the whole enormous structure from the ever-present threat of corrosion. The bigger the turbines, the fewer you have to install and maintain.
“Right now, the offshore models are starting at three to four megawatts,” Schkoda says, “and the prototypes are in the eight-megawatt range. You just have more wind out in the ocean, and you don’t have as many things around, so you can put a larger machine out there. But the drawbacks are that it’s a harsher environment, more humidity, more salt, harder to install.”
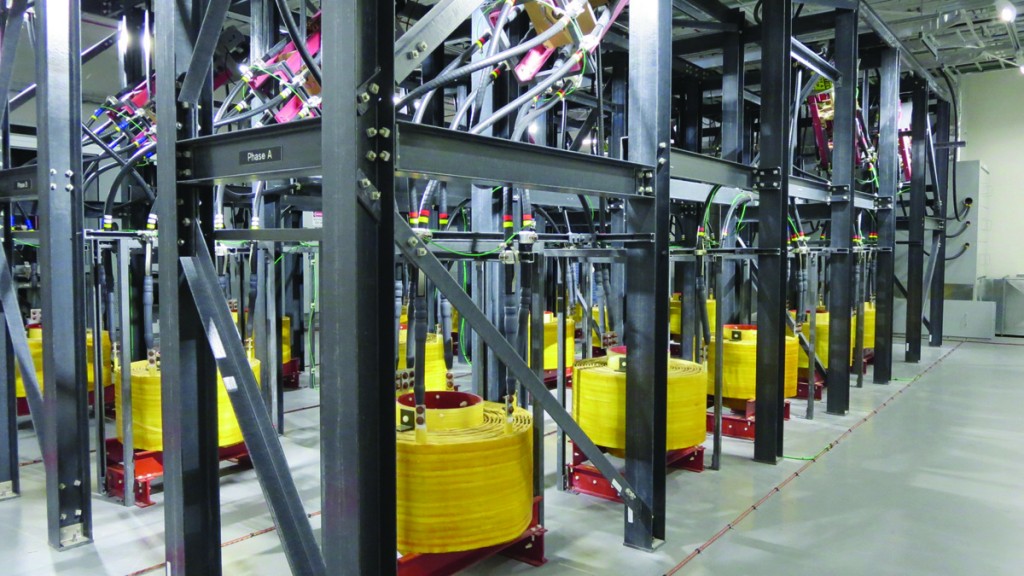
Air-core inductors, coiled in yellow insulation, simulate events on a large power grid. Photo by Ryan Schkoda.
Gearing up for a dry run
But an even more significant barrier to large turbines may well be the problem of predicting their performance and durability. When you design a big, expensive new prototype, how do you test it?
You probably can’t afford to install it and then wait a few decades to see how it reacts to all possible weather events, including hurricanes. You have to know pretty well what to expect before the you-know-what hits the fan.
“The problem with prototyping a wind turbine and putting it out in the field for testing it is that you may not acquire a lot of useful data,” Schkoda says. “First of all, we don’t have an efficient way to measure a wind field. The response of the wind turbine depends on the entire wind field, not just the average speed, which is typically what is measured. Also, it’s the turbine’s response to extreme or rare events that engineers are particularly interested in, which by definition are rare. So even if you wait six months or a year you may not observe the type of scenario you’re hoping for, and if you do, you’re going to get it once, and that’s it.”
Even if your company could afford to wait a hundred years for a hundred-year storm, you still wouldn’t collect enough data from a single event to learn everything you needed to know about what happened inside the machine, Schkoda says. So Clemson and its partners have attacked this problem by building a pair of test bays, each with a gigantic socket into which the team will plug a nacelle—a unit that includes the turbine’s housing and internal working parts, intact except for blades and a rotor. The team will apply power, and spin the drivetrain at various speeds and torques, under various kinds of mechanical stressors and loads. They will use sensors mounted throughout the nacelle, along with computers logging data in the control rooms, to monitor what happens every step of the way.
“Operating the turbine in a laboratory setting versus in the field offers a big advantage in terms of data acquisition,” Schkoda says. “We have, in total, seven hundred and fifty channels of low-, medium-, and high-speed data acquisition available on each test bench. Acquiring this quantity and quality of data in the field is far more difficult than on a test bench.”
Testing, beyond the routine
So this is one big part of Schkoda’s job: to make sure the software he’s crafting can detect what’s happening, moment by moment, in a futuristic wind machine. How does the shaft react to a sudden change of torque? How are the teeth in the gearbox meshing, as the speed drops or rises? Are the onboard controllers reacting fast enough to adjust the pitch of the blades for the changing direction and force of the wind?
Dozens of variables like this affect the turbine’s performance, the wear and tear on its parts, and the payoff in usable power. So Schkoda studies the whole system, along with its parts.
“We look at how the main shaft interacts with the bearing, interacts with the gearbox, interacts with the generator, because you won’t be able to see that just by looking at gearbox testing at the gearbox manufacturer or main-bearing testing at the main-bearing manufacturer. You really have to get them all together, and you have to stress the whole nacelle to see how it responds.”
Some of the stresses and loads are routine. The industry prescribes various benchmarks that turbines must meet before they’re ready for a wind farm. These test protocols, Schkoda says, usually involve applying static or slowly varying loads. But the real world of weather is never so neatly prescribed.
“A wind turbine operates in a very dynamic environment, and the failure modes we’re seeing in the wind industry reflect that fact,” Schkoda says. “At the testing facility we can replicate this dynamic environment by controlling the wind, so to speak. We can drive the turbines statically and dynamically, replicating the loading scenarios it sees in the field.”
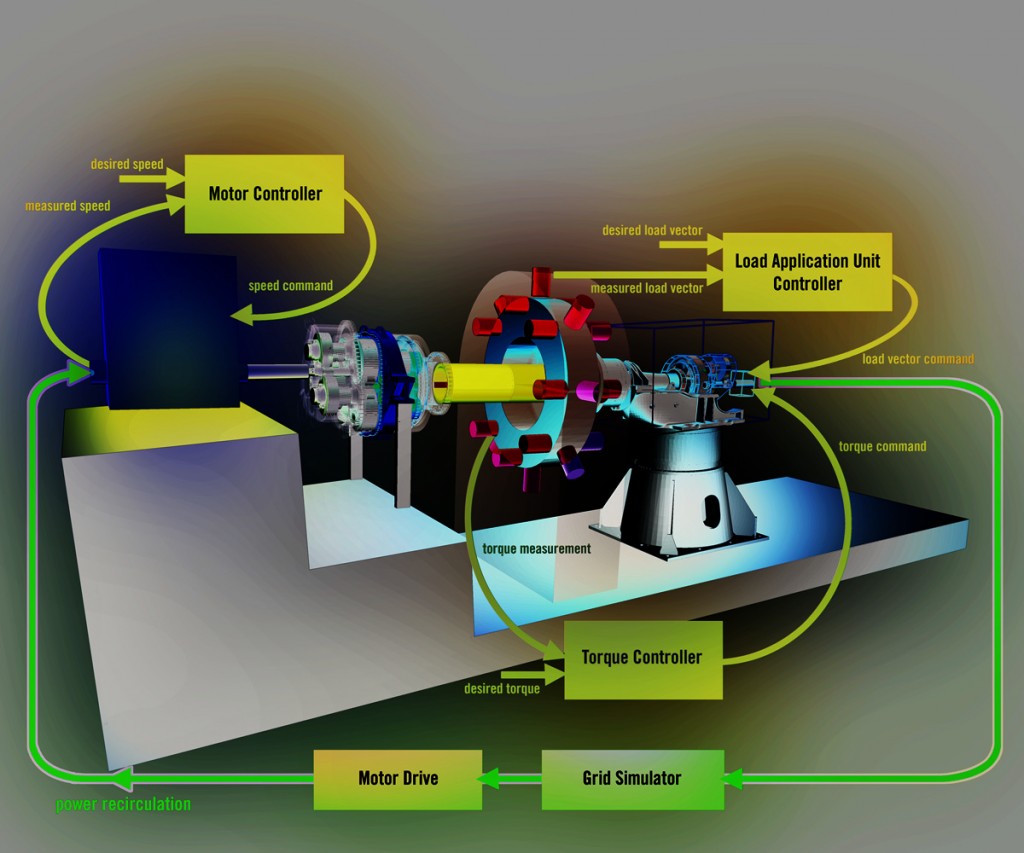
This simplified model of the test bench illustrates how power and data flow to and from each major component of the system. Illustration by Neil Caudle adapted from Ryan Schkoda.
Unpacking a lifetime of weather
So another part of Schkoda’s job is to learn how to stress the nacelle in all kinds of highly realistic, irregular ways, and that presents an even more formidable and intriguing set of problems.
How do you simulate, in the circuits of computer and a few million lines of code, the forces of nature? How do you compress, into weeks or months, several decades of simulated weather events?
Schkoda hands me an orange hard hat and leads me into the “multibody simulation lab,” a room equipped with racked CPUs and several monitors. There he introduces me to Amin Bibo, a member of his team.
“The idea here,” Schkoda says, “is to give test engineers, test operators, and customers the exact same interface to either of the two test benches that they would have in the control rooms, but in a simulation environment by replacing the physical equipment with real-time simulation models. This gives us an opportunity to study proposed test profiles and evaluate the simulated system responses prior to attempting anything on the actual test bench.”
He allows me to fiddle with the controls, increasing the force and direction of a simulated wind. I can watch, on the monitor, an animated graphic of a nacelle, accurate to its last detail, reacting to the forces I am wielding on a whim, like some pitiless wind god from Greek mythology. As the wind speed increases, the nacelle on my screen reacts. Virtual controllers adjust the pitch of virtual blades to maximize energy capture.
“You never have a nice, beautiful, uniform flow coming into the wind turbine,” Schkoda says. “It’s always going to be at least a little turbulent, meaning you’ll have an imbalance on the rotor. One of the things we would like to study at the facility is this imbalance and how to mitigate the resulting loads so that wind turbines reach their design lives.”
Coding the known to predict the unknown
To simulate the whole range of possible environmental conditions, and their dynamic interaction with the nacelle, Schkoda creates computer-based models for each system of interest. The software tools he uses (including MATLAB/Simulink and SIMPACK) are standards in industries such as aerospace and automotive engineering; they help Schkoda model the complex interactions of multiple moving components. But there’s very little off-the-shelf software to help him simulate the special conditions of next-generation nacelles or the custom-built test benches his facility will use to evaluate drivetrains. For that, he has to fashion new models and write a lot of original code.
Over the last two years, Schkoda has been able to produce or acquire models of all the major components he’ll need to study each test bench. And he’s been using some of those models to help with the commissioning of the test bench—the rigorous period of testing and debugging that proves the system worthy and ready for business. For this phase, the guinea pig they’re using is a General Electric 1.6-megawatt nacelle, one of the company’s most popular units.
“We’re beginning to get data from the test benches and are using the data to validate the models,” Schkoda says. “We’re comparing side by side the predicted response of the model versus the actual response of the test bench. It’s very exciting.”
Once he’s sure that he has a good match between what his models predict and what actually happens on the test bench, he’ll begin to extrapolate, to model things that have not yet been tried on the bench, to predict what will happen during actual testing.

Five-megawatt turbines rise 500 feet above the waves in the Belgian part of the North Sea. Europe has a head start over the United States in wind energy, but Clemson’s new testing facility could help close the gap. Photo by Hans Hillewaert, Creative Commons.
Gaining on the competition
Schkoda leads me next into the control room, where a squad of engineers monitor computer screens adjacent to the 7.5-megawatt test bay. The General Electric nacelle, mounted a few steps beyond the glass of one wall, hums like a hive full of well-mannered bees. He shows me the test control station, where an operator can sit and ask for certain speeds and torques to be applied on the test bench. Down the way, computers acquire data, logging various measurements from the test bench and from all of the electrical systems in the building, to make sure the power’s flowing where it should. The room is configured so that a private company could set up its own equipment beyond a partition, to have whatever privacy it might need.
Once they commission the test benches and gear up for full-scale testing, Clemson engineers and corporate partners will run one of only two such facilities in the nation. The other site, operated near Boulder, Colorado, by the National Renewable Energy Laboratory (NREL), collaborates with Clemson to advance the science and engineering of wind-turbine drivetrains.
“We work closely with NREL to provide testing services that are valuable to the wind industry,” Schkoda says. “We collaborate on various levels to improve the testing capabilities available in the United States.”
Because of the facility’s dual role—academic research plus full-scale commercial testing and modeling—Schkoda, his colleagues, and their students all learn to work with a foot in each realm. They have to develop their research programs and simulation capabilities at the same time they’re wielding wrenches and screwdrivers, helping to install and commission the test bench.
Both roles are urgent because the U.S. wind-turbine industry can’t afford to lag in the field much longer. Europe, Schkoda says, is probably a decade ahead of the U.S. when it comes to incorporating wind into its energy portfolio, and several European countries have developed wind-turbine testing facilities. But Clemson, Schkoda says, will have the technology and the know-how to help American industry close the gap.
Guarding the data
We pass a room full of high-capacity servers awaiting rivers of data from the test benches, and Schkoda mentions the security measures required to protect the numbers.
“Those test results are very valuable to customers,” Schkoda says, “and we protect them accordingly.”
Clemson has contracted with Savannah River National Laboratories, which manages data security for nuclear facilities, to handle data acquisition and transfer. Encrypted data will flash through fiber-optic landlines to corporate clients or to Clemson researchers working on main campus.
Our last stop is the 15-megawatt drive bay, where we climb a set of steel treads to a catwalk and look out on a massive, gleaming disk studded with hydraulic actuators. The actuators will apply loads to the main shaft, when testing begins here. From this vantage point, the drive bay looks like a setting from science fiction. The building itself is a machine chock full of high-voltage electronics, seven half-megawatt motors to pump hydraulic fluid, and whole rooms full of switches, transformers, converters, filters, and more. When a big nacelle is up and running, the power it generates has to go somewhere, and in this case the operators have two options.
“We can either switch into the electric grid, and push that power right into the local grid, or we can circulate it back to the drive motors and recycle the power,” Schkoda says, “so that we only have to draw enough power to cover the losses due to friction and heat.”
The team can also model the turbine’s interaction with a power grid, using the facility’s in-house grid simulator, the Duke Energy eGrid, led by Clemson’s Curtiss Fox. Having the eGrid handy is a huge advantage, Schkoda says, because manufacturers and power utilities need to know how a new turbine will behave when connected to an actual grid. It’s not enough to test the nacelle in isolation, as a stand-alone device. You need to evaluate its performance as one node on a highly complex, dynamic network delivering power where people need it.
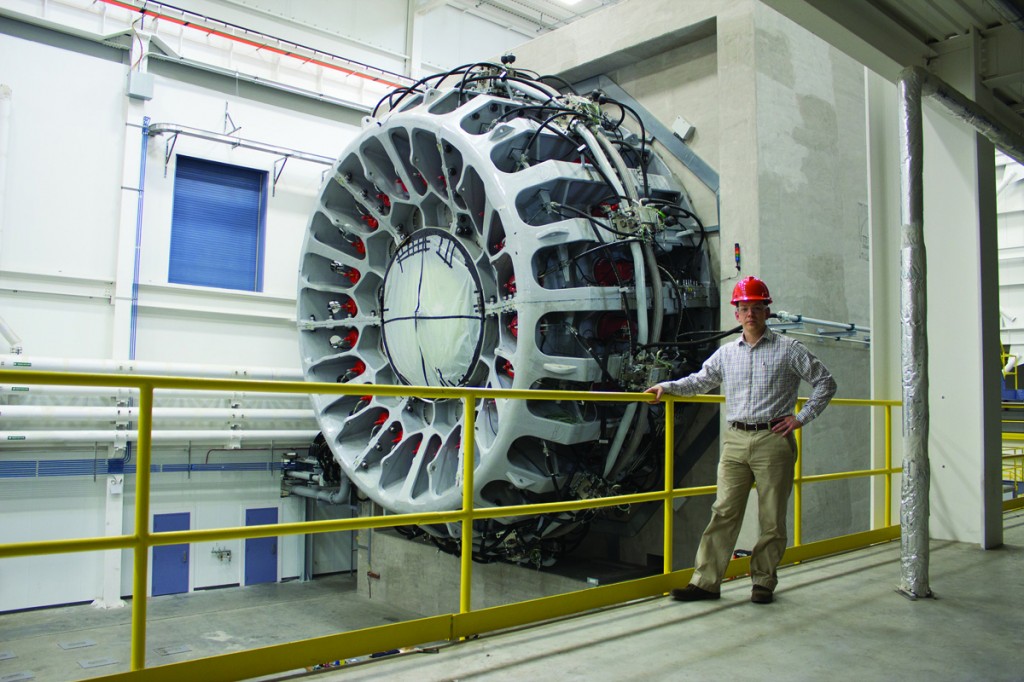
Ryan Schkoda in the 15-megawatt drive bay. Big turbines will yield more efficient power, if they can prove themselves on the bench. Photo by Neil Caudle.
Full circle
After we stash our orange hardhats and make our way back to the building’s front hall, we stop for a moment to look across the street at the Lasch Center, where the Hunley rests in its pool. One hundred and fifty years ago, state-of-the-art engineering produced an iron-hulled submarine powered by men turning cranks.
And here we are, only a few generations later, standing inside an enormous, machine-like facility that makes the Hunley seem as tiny as a wind-up bathtub toy. It’s a stark illustration of how far engineering has come.
“It’s unbelievable how much things have changed in only a hundred and fifty years,” Schkoda says. “As an undergrad I did an internship with General Dynamics Electric Boat and had an opportunity to work on our navy’s Ohio-class submarines. Comparing one of those ships to the Hunley really highlights that point.”
In the Hunley’s day, you heated your house with wood or coal. And you fired up your steam-powered sawmills and warships and locomotives with wood or coal. And you filled your lamps with oil. Because those were the machines of their era and the fuels available to hand. The windmills of the previous century? Gone.
But the wind has come full circle, here in Charleston. And wind machines may once again prevail. It’s the right city, at the right time, for an ambitious young engineer who’ll keep the lessons of history close at hand while he builds for the next hundred years.
“When I came here two-and-a-half years ago as a postdoc, this facility was a construction site,” Schkoda says. “It’s incredible to see what everyone’s hard work has been able to accomplish since then. We have a very talented group of engineers working on the project and the facility has come together beautifully. This is a very exciting time for all of us, and we’re just getting started.”
Clemson’s wind-turbine drivetrain testing facility is one step toward building a national powerhouse in renewable energy research and development. Next up? The sun.
Whatever the source of renewable energy, electrical power on a commercial scale moves on a grid.
Ryan Schkoda is a research scientist and a faculty member in mechanical engineering, College of Engineering and Science. He is based at the wind-turbine drivetrain testing facility, which was dedicated in 2013 as the SCE&G Energy Innovation Center, part of the Clemson University Restoration Institute (CURI).
Nikolaos Rigas, who helped lead the design and implementation of the center, is the executive director of CURI. Andre Mander is the director of operations for the center, which received a grant of $45 million from the U.S. Department of Energy and substantial support from SCE&G, Duke Energy, the State of South Carolina, and other public and private contributors.
The team operating the wind-turbine drivetrain testing facility includes a director, two test engineers, an electrician, a machine specialist, a postdoctoral fellow, and Schkoda. This team collaborates closely with the eGrid team, which includes a director, three research scientists, and an engineer, to “push the equipment and advance the state of the industry,” Schkoda says.
The title of this article, “Defining the Wind,” is borrowed from Scott Huler’s book about the Beaufort scale of wind measurement (Crown Publishers, 2005).